Smoother, Faster Bottle-Filling Workflow
In the realm of industrial automation, efficiency and precision are key factors that can make or break a production line. The ability to seamlessly transport products from one operation to another is crucial in ensuring a smooth workflow and maximizing productivity. That’s where the Mini-Mover Lite Series conveyor comes into play.
The Mini-Mover Lite Series conveyor serves as an essential transport platform, enabling a seamless movement of bottles from one operation to the next. It acts as the lifeblood of the entire assembly system, ensuring that the bottles are precisely and efficiently transported throughout the automated operations.
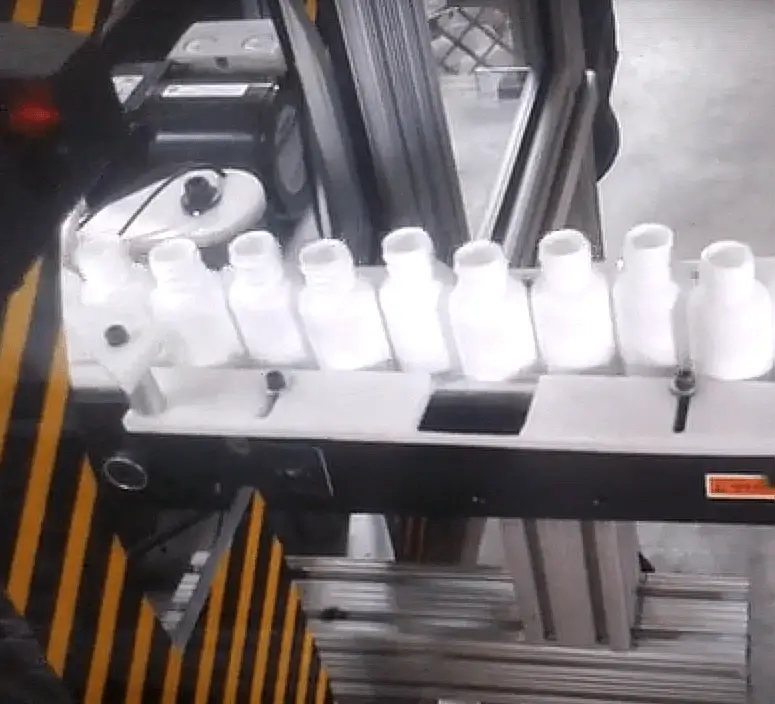
Speedy Bottling-Capping System with Mini-Mover Lite Series Conveyors
One of the primary advantages of using these conveyors is the elimination of bottlenecks and delays. In a traditional manual setup, there is always a risk of human error, which can result in production delays and even safety hazards. By automating the bottle infeed process using the Mini-Mover Lite Series conveyor, the risk of such errors is greatly reduced, leading to a more streamlined and efficient production line.
Additionally, the Mini-Mover Lite Series conveyors are designed with durability and reliability in mind. These conveyors are built to withstand the demands of a high-volume production environment, ensuring long-term functionality and minimal maintenance requirements. This robust design not only increases the lifespan of the conveyors but also reduces the risk of unexpected breakdowns, leading to uninterrupted production cycles.
The discharge process is equally important in maintaining a continuous workflow. After the bottles have undergone several automated operations, they are smoothly and efficiently discharged via another Mini-Mover conveyor. This seamless transition ensures that the bottles are moved out of the assembly system without any disruptions, allowing for a constant flow of production.