Repair, Retrofit or Replace?
Conveyors and pickup trucks have these expectations in common: We expect them to start right up every time; do the work they’re intended to do, without hiccups; and be easy to maintain over the years.
We can’t speak for pickup trucks, but Mini-Mover Conveyors builds its products for durability, reliability and a long working life. While taking into account usage factors, such as the type of product, the operating environment and average run-time per month, Mini-Mover conveyors and rotary table accumulators can and do last for a decade or more.
But there does come a time when a piece of older equipment begs the question: “When’s enough, enough? Repair, retrofit or replace?”
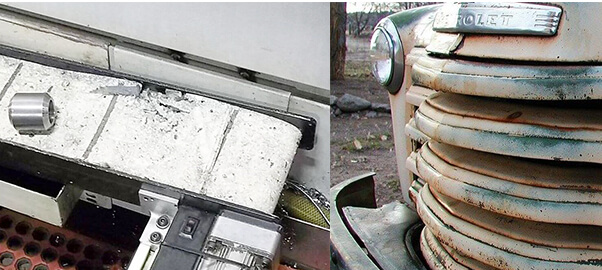
Easy Mini-Mover Fix with a New Belt. We Can’t Speak for the Truck
Repair (Maintenance)
Regular conveyor maintenance intervals can help ensure smooth, dependable operation over time. Scheduled maintenance reduces the chance of unplanned or emergency downtime and lost production.
But even with routine preventative maintenance, some components will eventually show signs of fatigue or wear. Moving conveyor parts such as the belting and pulley assemblies are essential to inspect regularly. If your conveyor is in everyday, steady use — especially if in a bottleneck operation — it’s best to replace an affected part during that scheduled maintenance interval. Waiting until something breaks means unscheduled downtime and disruption to production.
Scheduled maintenance periods should reflect the usage of your conveyor and your production dependency on it: is it integrated into a larger, throughput-critical cell? Does it run daily for more than one shift? Does your product operation create significant heat or debris? Factors such as these help determine its scheduled maintenance intervals.
And don’t skimp on pre-shift inspection. Proper belt tracking and tension makes the conveyor operate smoothly at full torque, while minimizing undue strain on the gearmotor and pulleys.
Many of our customers keep a small stock of common maintenance parts — belts or pulley assemblies, for example — in their tool cribs. Others keep complete spare conveyors, and do hot-swaps during maintenance activities. The plan, in both cases, is to minimize real or potential downtime.
Yet, one of our customers decided maintenance might be needed for his LP Series Mini-Mover Conveyor after “running it continuously for 8-12 hours a day, 5-6 days a week for about 5 or 6 years.” We don’t suggest this, but it does show that our conveyors can hold up to a lot of heavy use without being pampered.
Retrofit
Floor plans change. Machining jobs — parts, assemblies, processes – change. This can create a need to reconfigure many pieces of existing plant equipment, including the conveyor. Perhaps a new job requires more grip, impact protection or product separation as the conveyor handles parts. Often, with a simple retrofit in the conveyor’s belting material or by adding cleats, the issue(s) can be solved.
Perhaps new clearance requirements are needed for a larger product, or changes to machine’s setup creates a clearance issue. A retrofit of the conveyor’s drive-package orientation can often solve it. Need a faster or slower belt speed? A simple gearhead retrofit is easy to do. Mini-Mover Conveyors offers a wide variety of accessories as well, which can help reconfigure the conveyor to a new or revised production task.
But if the scope of changes you need are very extensive, it’s important to compare the cost of the retrofit parts vs. the cost of conveyor replacement.
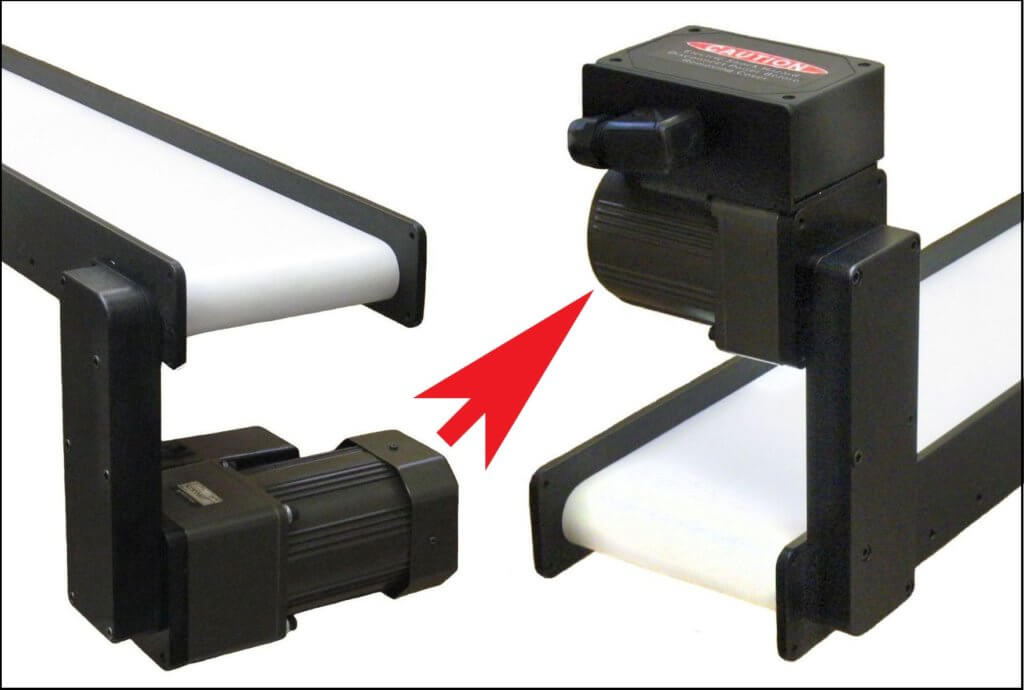
Field Retrofit of Mini-Mover Drive Mount and Gearmotor
Replace?
Most Mini-Mover conveyors stay reliably in service for a decade or more without heroics. That being the case, these conveyors often outlive the job(s) they were originally purchased to do. Replacement would be a reasonable option if no amount of retrofitting would result in the new configuration you need. For example, if you need a conveyor that’s far bigger or smaller than what you have, then replacement makes sense.
What about a damaged conveyor? Or one that’s gone years without routine maintenance? First, assess the extent of the damage. It takes a lot of beating to make a Mini-Mover Conveyor unfixable. Get a cost estimate of repairing or retrofitting the damaged components, and compare this to the cost of total replacement. Sometimes, a repair better fits the budget; sometimes replacement is more cost-effective in the long run.
How Do I Decide?
It’s best to have a plan in place, long before you reach this decision point. Your department or company may already have budgetary, safety and maintenance policies that can guide your choice. There’s just no generic magic formula that can reasonably apply to all conveyors, because no two production situations across the manufacturing spectrum are exactly the same.
Free consultations are always available from Mini-Mover Conveyors. We support our products throughout their lifetime, stock commonly used maintenance components and offer no-obligation applications advice. We seek always to keep you up and running – and help you choose the most prudent product option to suit your budget and long-term production needs.